Pushing the limits
SEG Automotive optimizes temperature models for high-voltage e-machines using NEWTWEN's digital twin technology, Virtual Thermal Sensor (VTS).
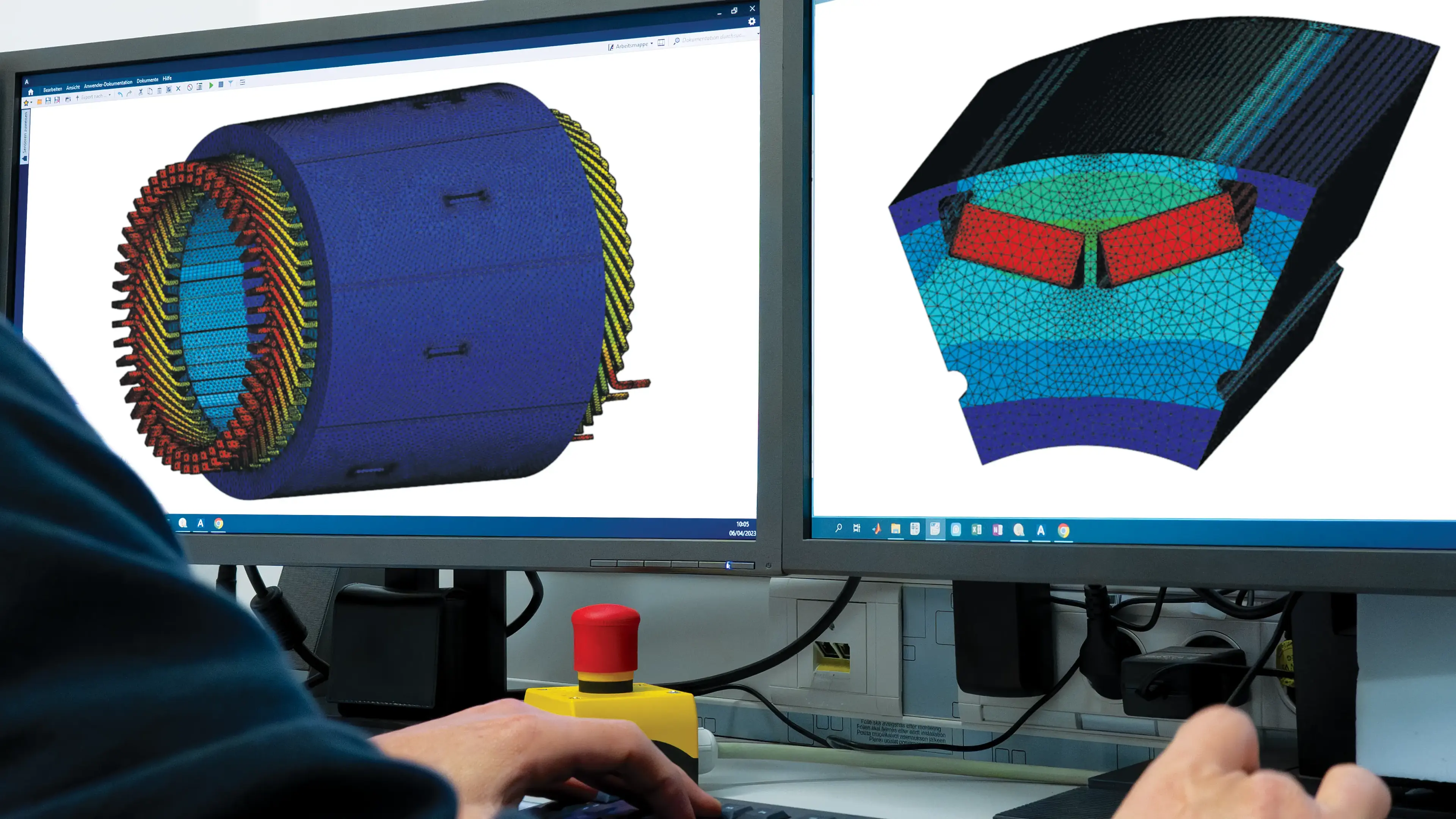
The decisive factor for the use of electric motors in modern vehicles is their efficiency. It determines performance and, above all, the range that can be achieved with one battery charge. Among other things, efficiency is influenced by the temperatures inside the machines. If this is not precisely known, it cannot develop its full power, as the load must be reduced at an early stage to protect it. In the worst case - if the temperature is underestimated – the machine may even fail prematurely or even be damaged. To keep the temperature low and thus ensure the highest possible continuous performance, e-machines are cooled - with air, water, or oil.
But how much cooling is needed where on the machine and how can the system weight be kept to the necessary level? How can the highest possible power density be achieved? Answers are provided by temperature models obtained from measurements - or from simulations. In cooperation with [Opens in a new tab] NEWTWEN, SEG Automotive has developed a digital twin for its own e-machines that helps to precisely answer these questions on a simulation basis.
Founded in Italy in 2020 as a spin-off from the University of Padua under the name Hexadrive Engineering, NEWTWEN has rapidly become a leading reference in the automotive market for the thermal management of ePowertrain components. The company develops advanced software solutions for the electric drive and automation industry that can quickly and automatically generate virtual thermal sensors. So far, however, the company has not been active in the field of e-machines themselves, but has acquired references in inverter protection, for example. The cooperation with SEG Automotive is therefore a win-win situation: we can improve our temperature models and NEWTWEN can also extend the virtual thermal sensing technology to e-machines and form a reference here.
Virtual Thermal Sensor (VTS)
A Virtual Thermal Sensor (VTS) is a software solution that accurately estimates the granular thermal behavior of a component in real-time across all its operating conditions and lifetime.
Up to now, we have typically investigated the thermal behavior of our machines during development using complex FEM/CFD(1) simulations and physical measurements on the machine itself. However, these analyses take several days to calculate. In addition, the measurements include more data than is actually required. The extreme points are particularly important for the load behavior. Thermal protection for our electric drives therefore requires models that can be executed live on the microcontroller (µC) of our machines and monitor the temperature exclusively for these critical points.
NEWTWEN's digital twin, VTS, also uses artificial intelligence (AI), which performs a plausibility check of the model parameters against real measurement data and thus independently optimizes the model. On the one hand, the tool identifies relevant hotspots so that the protection of the machine can be focused on the hottest point. On the other hand, we reduce the complexity of the model while maintaining the best possible temperature accuracy in the relevant hotspot.
(1)
FEM: Finite Element Method,
[Opens in a new tab]
Finite element method - Wikipedia
CFD: Computational Fluid Dynamics,
[Opens in a new tab]
Computational fluid dynamics - Wikipedia
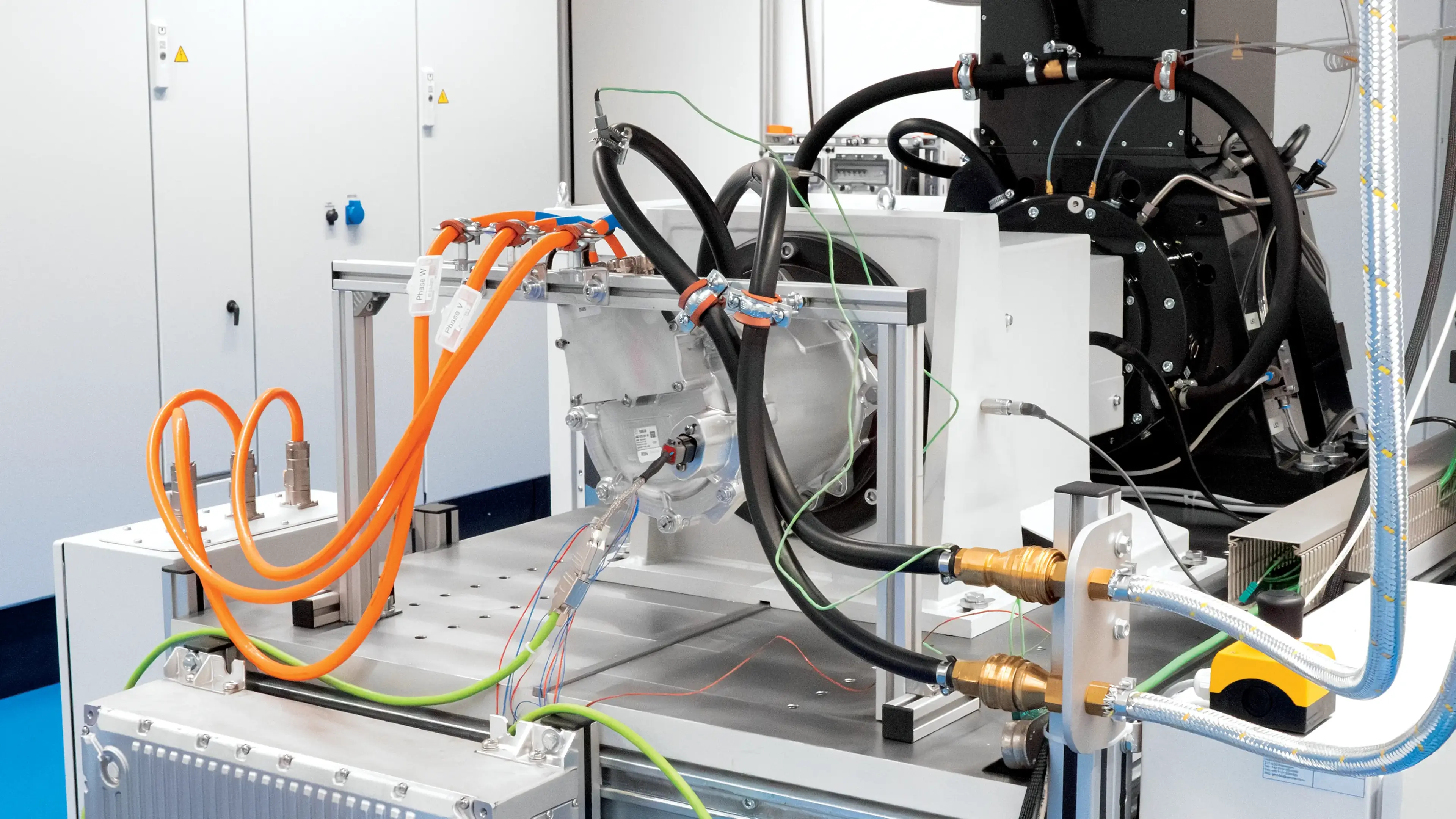
Better predictions thanks to precise temperature models
The knowledge gained enables us to derive a better estimate of achievable accuracies for customer acquisition. Our customers often demand exact statements or specify values. By using the tool, we can reduce our risk, which previously existed due to the use of assumptions. Furthermore, the models are so interesting for customers that it is conceivable to offer them as additional added value. This would be an additional USP, especially if we only sell the machine and the system responsibility therefore lies with the customer: certain machine states could be mapped directly via the integrated tool without additional sensors. In the future, the AI function could even be used for predictive maintenance, i.e. the predictive maintenance of the machine. Finally, the power density of our machines can be improved using the knowledge gained.
The project team at SEG Automotive consists of experts in the fields of e-machines, systems, and software, who work closely with NEWTWEN's experts in numerical simulation and optimization of electromagnetic systems. While the pilot project will initially be implemented in Europe, the findings can also be transferred to our global high-voltage development.
"The digital twin helps us enormously in the development of temperature models! Compared to the previous simulation methods, we can achieve more precise values more quickly. This helps us to optimize our e-machines, which ultimately benefits our customers. We appreciate the good cooperation with NEWTWEN and are pleased that we can make our contribution to improving the Virtual Thermal Sensor in return," says Rüdiger Benz, Head of Development at SEG Automotive.
The project started in 2023 with the first prototype implementation. Subsequently, optimization approaches were discussed in close cooperation with NEWTWEN and checked by a validation measurement at the end of 2023. In 2024, we will now use the tool to evaluate different machines and check the results in comparison to the previous measurement method. We want to determine how accurate and flexible the tool is and how much time it saves compared to the previous procedure.
For NEWTWEN, the aim is to further improve its technology for real-time temperature monitoring, adapt it to customer needs and further optimize its user-friendliness.
“NEWTWEN is extremely proud to have worked alongside SEG Automotive on this project. We believe that virtual thermal sensing represents a solid foundation for the future of the industry. We are profoundly humbled by SEG Automotives commitment to pushing technological boundaries further, and we look forward to seeing the new heights this partnership will bring for both companies", says Francesco Toso, CEO of NEWTWEN.

Press contact
SEG Automotive
Christoph Hoelzl
Press Officer / Pressesprecher
Tel.
[Opens in a new tab]
+49 711 4009 – 8172
[Opens in a new tab]
press@seg-automotive.com