Magazine amz publishes interview with Michael Schedler, Head of Remanufacturing at SEG Automotive
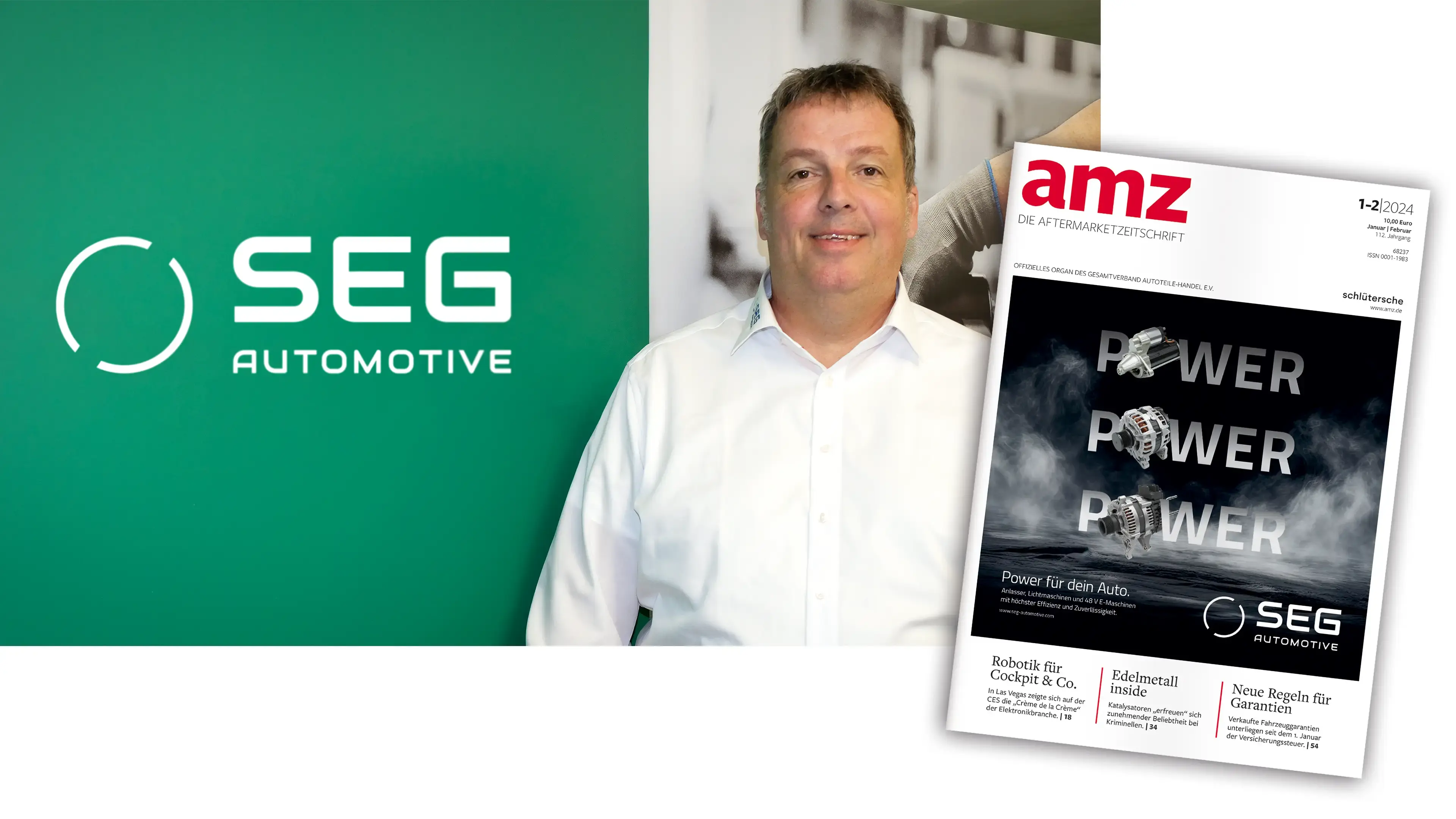
Michael Schedler, Head of Remanufacturing at SEG Automotive
"We will still need spare parts for hybrids until 2050," says Michael Schedler in his interview to amz - THE AFTERMARKET MAGAZINE, in which he talks about the transformation in the Automotive Aftermarket. Workshops are already forced to increasingly adapt to e.g. hybrid vehicles, as this solution is attractive due to increased environmental awareness, political climate targets as well as the tax advantage for company cars. The BRM (Boost Recuperation Machine) and its remanufacturing are decisive for this transformation. In the amz article, you can find out how this will change the work of workshops and what additional hurdles need to be mastered.
“We will still need spare parts for hybrids until 2050”
Article from Simon Bäumer, amz - DIE AFTERMARKETZEITSCHRIFT.
In addition to pure BEVs, it is primarily hybrid vehicles that are increasingly being found in workshops - the tax advantage of the 0.5% rule for company cars makes these variants attractive. In an interview with Michael Schedler, Head of Remanufacturing at SEG Automotive, we talked about the change.
Hybridization is also changing the auxiliary drive. Where the classic generator once worked, there is now a highly complex starter generator. The small but powerful electric motor turns the combustion engine into a hybrid, but presents manufacturers and the aftermarket with new challenges. The part is becoming more complex for the workshop, both in terms of diagnosis and replacement. "Simply" replacing the regulator is no longer an option - workshops are once again facing a major change.
Water cooling, inverters, vehicle-specific programming. How far-reaching will the changes in the auxiliary drive be for workshops in the future?
Michael Schedler: In this context, I would rather speak of a consistent further development towards electrification. Strictly speaking, it is a bridging technology that allows the classic combustion engine to be turned into a hybrid without any major conceptual adjustments. It is true, that the product is significantly more complex in terms of system integration and software control in application development. However, I don't see this as a major challenge for workshops. Linking a wide variety of components after a replacement is already part of everyday life - as is the case with programming engine control units and programming immobilizers.
To what extent will this also change everyday life?
Michael Schedler: The "Boost Recuperation Machine" - BRM for short - is a generator that now also functions as a motor and provides additional electric drive when required. Paired with a 48 V battery and the corresponding converter, the vehicle becomes a hybrid. Nevertheless, we are still operating in the low-voltage range compared to fully electric vehicles. This does not mean that everything is fundamentally changing for workshops, but the change is of course progressing.
Until now, most alternators were air-cooled - with the BRMs, water cooling is now the standard. How much power loss are we talking about here?
Michael Schedler: With the BRM, the electrical machine remains air-cooled, just like the alternator. There are differences in the inverter, i.e. the electronics. Depending on the application, this can be air-cooled or water-cooled for a higher continuous output. In terms of efficiency, the BRM is significantly better than "normal" generators at 84%, i.e. 16% loss. The average values here are currently between 70 % and a maximum of 80 % for high-efficiency generators.
How big are the changes for you in the remanufacturing of BRMs? What challenges does the new technology bring that didn't exist before?
Michael Schedler: Remanufacturing electronics has always been a challenge for repair, let's think of control units and infotainment. You can no longer simply rework or replace components, as we know from mechanical components. Instead, it is important to use intelligent test programs to identify possible hardware-related malfunctions and sort them out accordingly. All software problems are then rectified by installing the latest programming as standard. In our case, there is also the mechanical part, but its preparation is less of a challenge. The pitfalls lie more in the interaction between the electronic and mechanical parts.
In Treto, Spain, you are one of the few manufacturers to carry out remanufacturing on the same production lines as new production. How great are the synergy effects that you can achieve as a result?
Michael Schedler: We rely on capacities, production lines, tools and the expertise of employees from series production. The synergy is still manageable when it comes to dismantling and cleaning the old parts, as this step is not involved in new production. However, we can draw on testing and production steps from series production for the diagnosis and reworking of the components. In the final assembly of the components, the synergy effects are almost 100%. Here we use all existing systems and test equipment, including the final test at the end of the line. As a result, we achieve the same quality in remanufacturing as in new production - and that clearly sets us apart from the competition.
What were the biggest challenges in setting up BRM remanufacturing?
Michael Schedler: The core challenge is the same as with other products: What is the most effective way to disassemble the parts so that we can reuse as many of them as possible? On top of this, however, comes the interaction between software and mechanical parts, for which we at Treto can count on the specialist staff from series production.
There is currently a great deal of remanufactured goods of various qualities on the market. Do you think that the more complex technology will lead to consolidation, because not every supplier will be able to remanufacture such complex units?
Michael Schedler: It will certainly raise the bar considerably. Not every smaller company will be able to afford the measuring and programming equipment and the development costs for the associated software. But here, too, there will certainly be one or two innovative repairers who specialize accordingly and can keep up with the change.
On the one hand, the OEMs' expectations in terms of quality and service life increase with each new generation of vehicles, while on the other hand, vehicles are being driven for shorter and shorter periods of time. If you compare the market with 20 years ago, how has the potential for aftermarket units (Reman and Newman) changed?
Michael Schedler: Despite the changes, the demand for spare parts has not really decreased over the years. Increasingly complex parts, the use of more electronics and dealing with them has certainly led to a certain degree of specialization and consolidation. Whereas 20 years ago it was still possible to repair one or two units, today this is hardly possible with simple means. As a result, a new or remanufactured part is likely to be needed more frequently in the event of a decline in damage. The higher the price of the component, the more likely it is that a reman part will be used. In addition, increased environmental awareness and political pressure towards a circular economy mean that I am not worried about the future of remanufacturing.
Should the ban on combustion engines remain in place in 2035, would SEG Automotive then convert the production sites to exclusively remanufacturing plants? How long will there be a need for aftermarket units after the end of series production?
Michael Schedler: No, certainly not. Apart from the fact that we will still need spare parts for the aftermarket until at least 2050, our conversion to electrification is in full swing. We are already manufacturing motors for e-bikes in Treto and will start producing electronics for inverters at the beginning of 2024 as part of a massive investment. So change is not stopping at our plants, but we believe we are well equipped for the future.